In today’s Formula 1 landscape and indeed across other top-tier motorsport series, driver-in-the-loop (DIL) simulators have evolved from peripheral driver training tools into mission-critical components of performance development, writes Ian Haigh, solutions group manager at Ansible Motion
Just a decade ago, DIL simulators were used primarily for driver circuit familiarization and rudimentary setup work. Now, they serve as tightly integrated, virtual race circuits, capable of simulating aerodynamic upgrades, fine-tuning chassis setups and validating race strategies with remarkable fidelity.
In an era of restricted track testing and ever-increasing vehicle complexity, these simulators enable teams to iterate rapidly, with controlled, repeatable conditions that mirror real-world racing scenarios. Just look at how DS Penske is embracing multi-sim setups to consider drag and other inter-car factors.
But as engineers in the paddock know well, deploying a DIL simulator that actually delivers usable correlation is no easy feat. When it works, the rewards are substantial. When it doesn’t, the pitfalls can be costly.
A public admission
Adrian Newey’s recent appointment at Aston Martin Aramco Formula One Team as managing technical partner has come with characteristically candid assessments. Among the topics he’s addressed openly has been the shortcomings of the team’s DIL simulator program.
“I think it is fair to say that some of our tools are weak, particularly the driver-in-the-loop simulator. It needs a lot of work because it’s not correlating at all at the moment. It is a fundamental research tool – not having that is a limitation,” Newey said to The Race at the Monaco Grand Prix in May 2025. “But we’ve just got to work around it in the meantime and then sort out a plan to get it to where it needs to be. But that’s probably a two-year project in truth. So, we’re going to be a bit blind on that for some time. We have just got to try to use experience and best judgement. How successful that will be, time will tell.”
He added that while this two-year recovery process is underway, the team would have to lean heavily on engineering intuition and experience.
Newey expanded on this issue further on the Aston Martin F1 website, highlighting the interplay between hardware and modeling: “You can have the best motion system in the world, but if you don’t have the modeling to go with it, and correlation with the aero model, correlation with the tire model and so on, it won’t be of any use.”
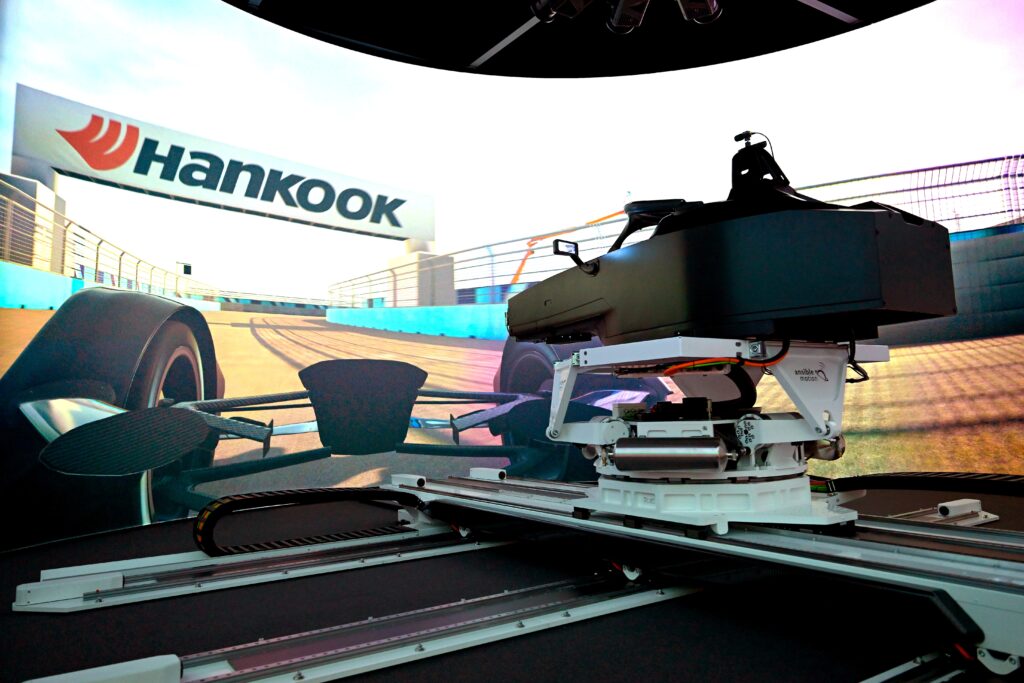
Copyright 2024 © Sam Bagnall
Correlation
Team principal Andy Cowell echoed Newey’s sentiments, noting that correlation challenges are widespread, even among the most seasoned outfits, and that the new simulator, commissioned in 2024 at Silverstone, would take time to dial in.
“I think whenever you create new equipment, it takes a while to commission it and then work out how well correlated either the DLS [Dynamic Lap Simulation] or the wind tunnel is with the real world,” he said in an interview with Sky Sports F1 . “So, you need to do some updates, bring them to the track, you need to see how everything matches up. That’s the correlation. And even experienced teams have problems with correlation. You hear it up and down the pit lane.”
Aston Martin is clearly responding. Part of the effort involves personnel changes, including the recruitment of simulation and vehicle modeling director Giles Wood, who was previously involved in autonomous vehicle programs at Apple, and Gioacchino Vino, both of whom bring experience from Newey’s Red Bull tenure.
While specific details about the simulator in question remain undisclosed, from our vantage point [at Ansible Motion], it pains us to hear comments such as Newey’s because we understand from experience, the scale of the challenge the team is facing.
Motion commotion
It seems that many early-stage assessments of DIL simulators focus on motion systems as defining the capability of a DIL simulator. Newey’s comment about “You can have the best motion system in the world, but if you don’t have the modeling to go with it … ” speaks directly to this point and it may indicate that the team fell into this subtle trap prior to Newey’s arrival.
Motion machinery is certainly a visually dominant part of a driving simulator installation and we know that automotive engineers naturally gravitate toward motion systems because they are more “relatable” than many of the other DIL simulator systems. But while it is certainly important, motion capabilities do not singularly define the quality of a driving simulator or its capacity for correlation.
DIL immersion is a multi-sensory endeavor and motion is just one of the players. In other words: motion is but one sub-category of one type of sensory stimulation that addresses just one category of human senses. If we stand back to look at DIL simulators from a big picture perspective, across the entire spectrum of correlation requirements, is motion cueing any more or less important than vision cueing, or auditory cueing or any other type of sensory cueing? Probably not. All of these sensory triggers must work together seamlessly, in a convincing way for driver and engineer.
A moving experience
It’s also worth noting that the purpose of a driving simulator’s motion machinery is not to move a car around or to replicate the motions of a real car. The purpose of the motion machinery is to move a human being around, to convince them that they are interacting with a real car. This is an entirely different task.
DIL simulator correlation – which Newey correctly identifies as the cornerstone to making progress – can therefore be a trickier proposition than might first be imagined. It starts by viewing the simulator as a whole – not just as a motion machinery kit – in the context of measurable driver interactions. We speak from experience on this, as we’ve been tackling it for over 15 years.
When we talk about correlation in DIL simulation, it’s not just about ensuring that the physics model aligns with telemetry. It’s about ensuring that the driver’s physical and cognitive responses in the simulator align with those in the real world.
From concept to practice
To make DIL simulators viable tools for strategic decision-making, whether for evaluating tire degradation, energy deployment or aerodynamic tweaks, teams must go well beyond basic hardware benchmarking. Engineers must grapple with multiple data streams:
Simulator platform telemetry – useful for understanding motion/vision cue tuning, but isolated from track-based comparison unless multiple simulators are in play.
Vehicle model outputs that can be compared to track data – such as velocity, longitudinal/lateral accelerations.
Model outputs that cannot be directly measured on track – for example, slip angles, damper loads.
Supplementary data – driver biometrics and neurophysiological feedback.
This makes DIL simulator correlation an inherently layered task. Newey is absolutely correct to say that modeling fidelity and how each sub-model integrates, is paramount. A tire model that is validated in isolation can unravel in the simulator if it doesn’t harmonize with the road surface or contact patch behaviour.
Real-world strategies for virtual validation
Here are a few practical techniques that have been shown to deliver results for race teams aiming to sharpen their simulator performance:
Steering histograms: Comparing simulator vs real car steering angle and torque distributions over several laps helps validate driver workload and consistency.
Sector-level analysis: Instead of focusing on full-lap comparisons, analysing key track sector, especially those with high tire load or aero sensitivity, can surface model discrepancies that affect lap time most.
Cueing vs physics overlay: Overlaying motion and vision cue commands against physics-based vehicle telemetry highlights delays or mismatches in the driver experience pipeline.
Frequency response characterization: Instead of relying on vague “bandwidth” metrics, teams should assess simulator channels across frequency ranges to understand how well they convey critical signals like tire chatter or aero buffeting.
Motion-vision latency matching: The timing relationship between motion and visual cues has a profound effect on driver immersion. Even sub-10ms mismatches can degrade realism. We recommend that teams independently measure latency rather than relying solely on vendor specifications.
As Cowell noted, “Even experienced teams have problems with correlation.” DIL simulation is not plug-and-play. It requires system-level thinking, an understanding of human sensory integration and a relentless focus on correlation across every component – from aero to tires, from motion to perception.
While Aston Martin’s current challenges are very public, they are by no means unique. But with the right investment, whether that’s in people, tools and process, they’re certainly solvable. After 15 years of focusing purely on this, we know that mastering the virtual world is often the key to mastering the real world.